Hydrographics
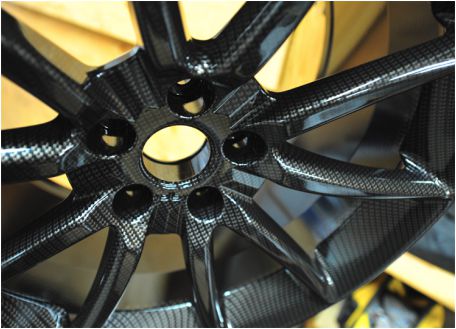
For nearly 20 years, B&I has been performing stunning part transformations with hydrographics (also known as water transfer printing, hydro dipping and immersion printing).
We began by servicing our automotive customers, applying woodgrain and carbon fiber finishes to parts such as floor consoles, dash bezels and engine covers.
As our reputation for producing high-quality hydrographics grew, we expanded into different markets, refinishing parts such as ski masks, generators and ATV body’s.
Today, we routinely process both low and high volume orders for customers in all industries, from automotive to marine to aerospace and more.
We provide order-specific solutions such as; custom jig creation, safe parts storage, special parts preparation and parts disassembly/assembly.
State-of-the-art equipment inside our 40,000 sq ft production facility and 17,000 sq ft warehouse, include multiple hydro dipping tanks, rinsing stations, spray booths, down-draft booths, prep rooms, UV curing ovens and more.
After nearly 2 decades of refinements to our water transfer printing process, we are able to consistently produce parts with the highest quality, delivered on-time and of course, priced right!
The Process
Immersion printing can be applied to most objects made from plastics, metals, ceramics, fiberglass, wood and even glass.
Parts must be properly prepped before they can be refinished with hydrographics. Most commonly, parts are thoroughly sanded, cleaned, primed and coated with a base paint.
A water-soluble film, containing a high-definition printed pattern (ie. woodgrain), is then placed in a water tank where it begins to dissolve (after it is sprayed with a special activator), leaving only the ink on the surface.
Next, the prepped part is fully immersed into the water tank, where the ink transfers onto the part almost instantly. The part is then removed from the tank, washed and dried.
Finally, the part surface is sprayed with our beautiful high-gloss or matt finish polyurethane topcoat, providing ultimate protection against scratches, fading, discoloration and cracking.
The transformation of the part after water transfer printing is truly remarkable, featuring new marketable appeal and added value.
QUALITY
To insure true premium quality, all parts that go through hydro dipping pass through multiple in-process inspection points as well as a thorough final inspection.
Patterns
In addition to our standard finish offering (which includes our most popular woodgrains, carbon fiber and camouflage patterns), we offer hundreds of different patterns that can be color-tweaked to your requirements. We also provide new pattern development.
Lead Times
Smaller orders for hydrographics are generally produced in 5-6 business days, once parts arrive at our San Diego warehouse. Larger orders are quoted on a case-by-case basis.
Quotations
Please contact sales@bitrim.com to discuss your next project today. For smaller orders, you can measure your parts and provide us with the dimensions for an accurate quote.